Workplace Scenario: Risk Assessment
Workplace Scenario: Risk Assessment.We’ve outlined a real-life scenario which shows the application of learning outcomes from different modules in the NEBOSH General Certificate syllabus.
This blog was updated in August 2022.
Studying for the NEBOSH General Certificate can be a challenge, but it can prove even harder if you don’t have any practical knowledge of a particular concept covered in the course. This can make it a struggle to understand how that topic can be applied to a real-world situation, or indeed appreciate how important it may be in protecting people at work.
To help you understand how key concepts can be applied in the modern workplace, we’ve outlined a real-life scenario which shows the application of learning outcomes from different modules in the NEBOSH General Certificate syllabus.
Learning outcomes and assessment criteria
NG1/IG1
Positively influence health and safety culture and behaviour to improve performance in your organisation.
3.3 Summarise the human factors which positively or negatively influence behaviour at work in a way that can affect health and safety
Do a general risk assessment in your workplace
3.4 Explain the principles and practice of risk assessment
NG2/IG2
7.2 Assessment of health risks
- Routes of entry of hazardous substances into the body
- The body's defence mechanisms
- Sources of information
- Limitations of information used when assessing risks to health
- Role and limitations of hazardous substance monitoring
For a complete guide on how to pass the NEBOSH General Certificate NG2/IG2 Risk Assessment, take a look at our blog.
Workplace Scenario
Background
The example refers to activities carried out at a scrap metal recycling facility. The facilities receive and recycle many forms of scrap metal (construction steel, copper pipework, washing machines, car parts etc.) and process these metals into reusable raw materials. The raw material is then supplied to steelworks and foundries to make new steel or metals.
One activity at many metal recycling facilities is known as hot/flame cutting, or “burning”. This involves resizing construction steel by manually hot cutting (or burning) the material into appropriate lengths using hot cutting equipment – usually an oxygen and propane cutting torch. This process, however, generates fumes as the steel melts, which not only contains fumes from the melting
This process, however, generates fumes as the steel melts. This not only contains fumes from the melting steel, but also fumes from any coatings or covering which is on the steel as the steel is hot cut. One such steel coating which is commonly found on old construction steel is lead-based paint.
Legal requirement
In the UK, exposure to lead is controlled by the Control of Lead at Work Regulations 2002, which set an “action level” and “suspension level” for the amount of lead allowed in the human body. This is measured by the amount of lead in either urine or in blood.
If lead levels reach the action level, the employer has to investigate why this has happened and try to reduce it.
On reaching the suspension level, the person has to be referred to an occupational doctor (or similar person) who will repeat the test. If this confirms the result of the first test, the doctor will usually decide that the employee should not carry on working with lead. Action must be taken on the doctor’s decision, and the employee will not be able to work with lead again or be exposed to it until the doctor considers it safe to do so.
Identifying the risk
At one particular metal recycling facility, the process of hot cutting was being used. The management at the facility had carried out a risk assessment for this activity and, as part of this risk assessment, personal measurements had been taken to determine the operator’s exposure to hot metal fume (including the exposure to lead fume).
Control measures
It was not reasonably practicable to prevent exposure by other means. So, in order to ensure that personal exposure limits were not exceeded, the risk assessment identified the need to select and introduce respirators to adequately protect the operator from the inhalation of metal fumes, including lead.
Appropriate respirators were selected and the operator was also trained in its correct use, it’s cleaning, storage and replacement of filters. Face fit testing was also carried out.
A programme of blood lead sampling was set up to regularly sample the operator’s blood for lead levels, to ensure that neither of the lead levels in the Regulations was being exceeded.
Further investigation
Not long after the control measures were introduced and the blood lead sampling programme put in place, it was noted that the operator’s blood levels went above the Action level set in the Regulations.
This caused the management at the facility to carry out a review of the risk assessment, together with checks on the respirator, and a repeat of the personal exposure measurements. All of these checks did not identify why the blood lead levels had increased.
It wasn’t until a supervisor suggested that the activity should be observed to establish how the task was being carried out, that the potential cause of the overexposure was identified.
Analysing human behaviour
On observing how the operator was carrying out the task, it was determined that the method of hot cutting the steel was indeed correct; the operator was correctly wearing all the required personal protective equipment. However, when observing what the operator did during breaks, or in between hot cutting different items of steel, the cause of the problem became evident.
One issue when working in a metal recycling facility and handling scrap metal is the issue of getting skin and hands dirty and contaminated from the material, even though appropriate gloves are provided and worn. The operator in question also smoked cigarettes, and these cigarettes he would make (or roll) himself.
When the operator was taking a cigarette break, or going for lunch, it was observed that his hands were highly contaminated. He wasn’t washing them before rolling and smoking his own cigarettes or eating his sandwiches, resulting in lead poisoning through poor hygiene practices.
The issue of personal hygiene was sensitively raised and addressed with the operator and blood lead levels began to decrease.
Conclusion
It’s clear that management at the facility had carried out a reasonable risk assessment, but had not involved the operator in determining exactly how the activity was to be carried out. Nor had they observed in enough detail how the task was actually being performed to determine if the risk assessment was adequate and the control measures were effective.
The example illustrates the importance of:
- The consideration of human behaviour in the way a task is being carried out.
- The involvement and observation of the person who is going to carry out (or is already carrying out) the activity in the risk assessment.
- Ensuring that all routes of entry are taken into consideration (both theoretical and actual) when carrying out or reviewing a risk assessment relating to the exposure to hazardous substances.
Our NEBOSH General Certificate course provides both the knowledge and skills to assist employers in conducting a workplace risk assessment. Click to button below to view the product page!
Related Blogs @Model.Properties.HeaderType>
Real Life Stories
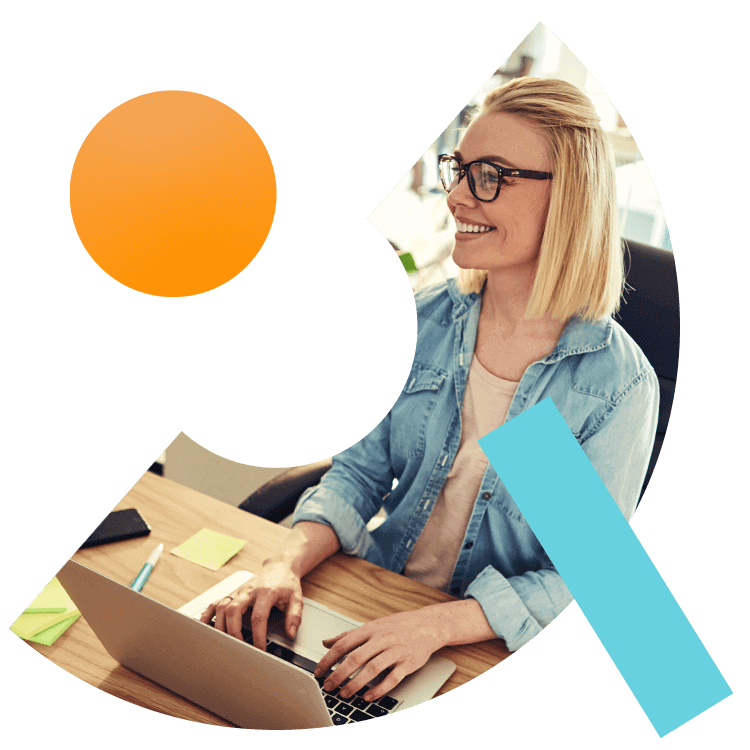